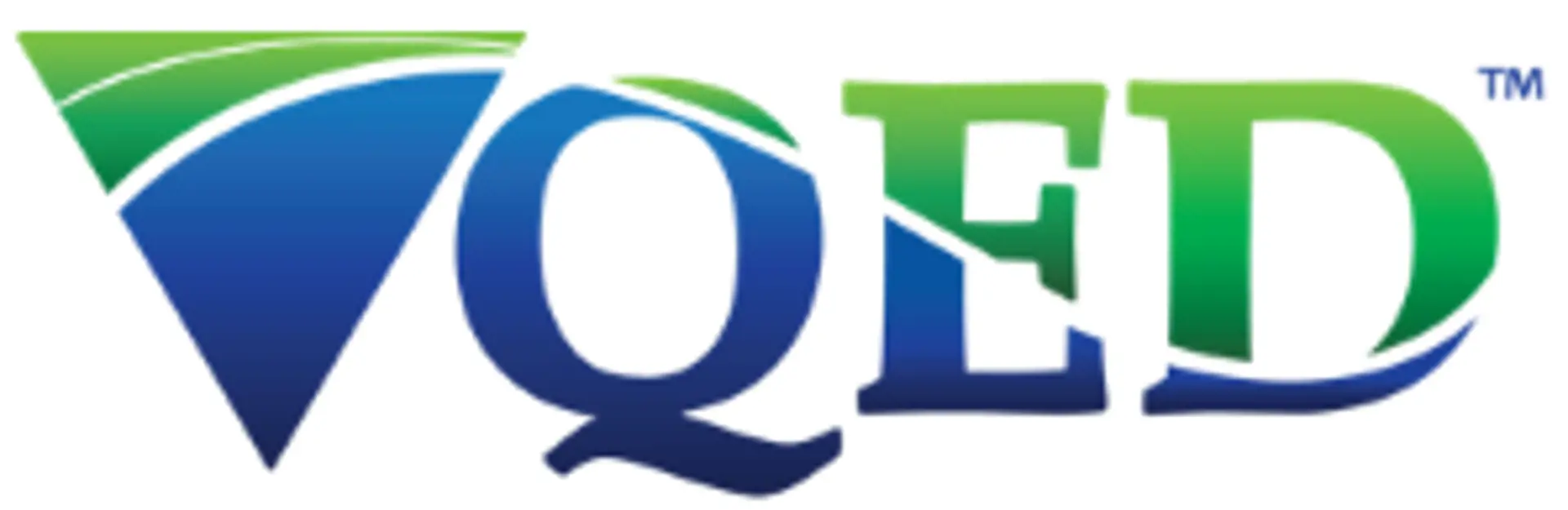
SteamTech Inc. of Bakersfield, California, a 35-year-old firm with roots in the oil field industry, is working for Bechtel-Jacobs at the Gaseous Diffusion plant in Piketon, Ohio. Bechtel-Jacobs considered several innovative remediation technologies and chose the steam injection process developed by SteamTech in conjunction with individuals associated with the University of California, Berkeley. The DOE is evaluating the process on a small contamination plume at the Piketon facility, a uranium enrichment plant with an old plume primarily consisting of TCE, PCB, grease and oil. The contamination exists at a depth of about 30 feet in a low permeability shale layer. The soils are very tight, which makes recovering the contamination difficult with traditional techniques.
The DOE learned of SteamTech's capabilities from a central California creosote project. SteamTech recovered more than 100,000 gallons of creosote from a depth of 150 feet utilizing their steam injection technology. Bechtel-Jacobs felt that if SteamTech could recover creosote from 150 feet, they should easily be able to handle TCE/PCB oils at 30 feet.
According to Hank Sauers, President of SteamTech, a critical element in the success of the Ohio system is the use of a durable downhole pump. SteamTech is using QED's AutoPump®, which is air-powered, constructed of stainless steel and other resistant materials, and able to operate in very harsh conditions. Sauers says, "Being from the oil patch, we like things that are rugged and simple. When I first took the AutoPump apart, I knew we had a winner. It's so simple and there's really nothing that can go wrong with it."
SteamTech is using a series of wells within a one-acre plume to extract the contamination. The wells are used for soil vapor extraction, water extraction and steam injection. Because the AutoPump is capable of handling high solids, high temperatures and frequent stops/starts, SteamTech can inject steam, at a temperature of 230-250° F into a well that already has an AutoPump installed in it! This is a tremendous advantage because it greatly increases the number of injection points and gives project managers greater flexibility in terms of mobilizing equipment.
Ready to take control of your environmental monitoring? Get in touch with QED today.